What is an electrical drive?
A drive operates and regulates the direction, speed, and torque of moving things. Drives are typically used in applications that require speed or motion control, such as machinery, transportation, robotics, fans, etc. Electrical drives are those that are employed to manage electric motors.Drives may be either constant or changeable in nature. The variable speed drives are employed in these situations to run the loads at any one of a large range of speeds because the constant speed drives are inefficient for variable speed operations.
Why are electrical drives necessary?
For precise and continuous control of the speed, location, or torque of various loads, adjustable speed drives are required. Drives with adjustable speeds are used for a variety of reasons in addition to this crucial function. Some of these consist of
To be highly effective: Electrical drives permit the utilization of a wide range of power, from milliwatts to megawatts for different speeds, reducing the system’s overall operating costs.
To improve the motor’s ability to stop quickly and accurately when reversing
To regulate the initial current
To offer the necessary safety
To set up complex control using different parameter values, such as temperature, pressure, level, etc.
Modern electric drives are more compact, efficient, less expensive, and perform better than bulky, expensive conventional electric drive systems that use multiple machines to produce the variable speed. This is due to the advancement of power electronic devices, microprocessors, and digital electronics.
Electrical drive technology
Electrical drive technology translates the resulting force into motion by converting electrical energy from the power supply system or from a battery into mechanical energy. Without electric drives, many devices that simplify our daily lives—such as elevators, escalators, gate drives, washing machines, mixers, electric razors, etc.—would not be possible. Both the megawatt and the microwatt markets have them, for example in wristwatches and applications like locomotives.
Furthermore, electrical motor technology has become crucial to industrial production. It is essential to the machinery and facilities used in the region’s industrial and logistical systems. We can suppose that the majority of our overall electrical energy is used by electrical driving technology.
Industrial components in electrical technology
Since the very beginning of electrical drive technology, electric motors have been the main source of power for machines. Along the way to current plant and automation technology, more and more elements have entered the picture. A gear unit located after the motor serves as a mechanical converter by adjusting the constant speed and torque given by the electric motor to the necessary levels in accordance with the demands of the machine or system to be operated. Typically, the electric motor is an AC motor. Electric motor and gear unit components come together to form a small unit in gearmotors.
As plant technology becomes more complex, so do the demands put on electrical drive technology. The majority of procedures also need that the speed can be converted and controlled. By converting the frequency and amplitude given by the power supply system, a frequency inverter—which is placed upstream of the electric motor—can be used to change the rotational speed and direction. The direction and speed thus become variables that can be controlled, allowing for the regulation of certain operations in driven machines and conveyor lines.
Nevertheless, the range of contemporary electrical drive technologies is far from full. The lines separating automation and driving technology are blurry today. By stopping system motions while the drive is not in use, brakes increase safety. Encoders that are attached to the motor continuously calculate the movement’s primary characteristic characteristics, such as its speed, torque, and current position. Processes are controlled by powerful electronics, control technologies, and software, according to the complexity of the system and its requirements.
Almost every area of modern life is impacted by electric motors. Electric motors are used to transform electrical energy into useable mechanical energy in a wide variety of appliances and gadgets, including refrigerators, vacuum cleaners, air conditioners, fans, computer hard drives, automated automobile windows, and many more.
Electric motors are used to power many of the everyday items we use on a daily basis, as well as a significant number of industrial activities.
Almost every product that can be made in a contemporary factory uses an electric motor at some stage in the manufacturing process.
It is not difficult to believe that there are over 700 million motors of various sizes in use worldwide due to the practically infinite variety of applications for electric motors. Because of how much electricity they utilize, the world is significantly impacted by this large number of motors and motor drives.
In the past, electric motors were regulated by extremely ineffective, expensive, and wasteful technologies. Modern ASDs were developed in recent decades as a result of the increased demand for performance and accuracy in electric motors, as well as the improvement of solid-state electronics and the low cost of microprocessors.
A system known as an ASD includes both a drive system and an electric motor.
The power source, the power electronic converter, the electric motor, the controller, and the mechanical load are the five components that make up any adjustable speed drive.
The system’s source of electric energy is the power supply. Any voltage level of electric energy can be supplied by the power supply, whether it is in the form of AC or DC. The link between the power source and the motor is provided by the power electronic converter. This interface enables the use of almost any electric motor with almost any power source.
The controller is the circuit in charge of regulating the output of the motor. This is done by modifying the power electronic converter’s operation to change the frequency, voltage, or current sent to the motor. The controller may be as simple as a microcontroller or somewhat complicated. Contact us for more information on drive repair.
Is it important to replace an old motor drive?
Usually, but not always, the electric motor is a DC motor or an AC induction motor. The mechanical system that needs power from the motor drive is known as the mechanical load. The mechanical load could be anything that can be moved by the cyclical action of a rotating shaft, including fan blades, air conditioner compressors, conveyor belt rollers, and more.
Technology for electric motor drives is continually advancing and finding new uses.
Older electric motor drives are being replaced with more modern ones in order to improve performance, efficiency, and precision. Because they employ more powerful microprocessor or DSP controllers to monitor and control motor output, advanced electric motor drives are more precise. By utilizing more efficient electric motors and converter topologies, they also offer greater efficiency.
By leveraging better switching schemes to deliver greater output power while using lighter motors and more compact electronics, the more modern drives today also provide a performance gain. checking all the electrical panel cleaning, wire and other system components etc. Come to us and save your electronic equipment easily.
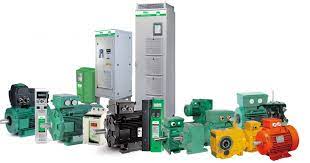
Avoid Downtime! Get Fast & Reliable Nidec Drive Repairs in Dubai
Nidec drives are essential components in modern industrial automation, ensuring smooth and efficient motor control. However, like any electronic equipment, they are prone to issues